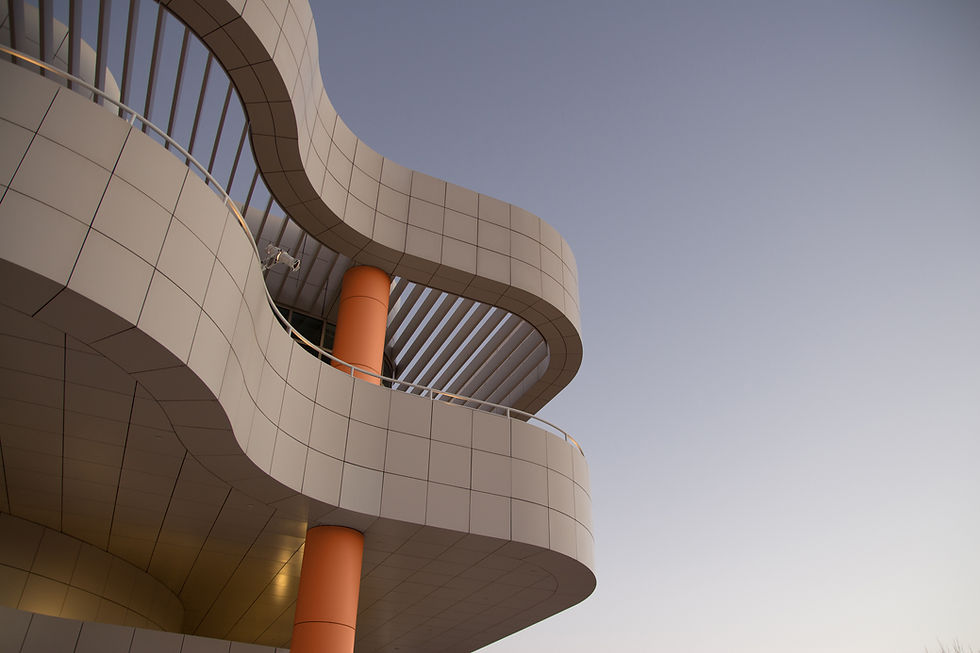
Why Precision Engineering Matters in Meso Needle Manufacturing
Mar 21
4 min read
0
2
0

Meso needles play a crucial role in aesthetic and medical treatments, particularly in mesotherapy, which involves the delivery of active ingredients directly into the skin. These ultra-fine needles must be meticulously crafted to ensure minimal patient discomfort, maximum efficiency, and superior treatment results. The precision engineering behind meso needle manufacturing is vital in maintaining consistent quality, safety, and effectiveness.
A reputable meso needle manufacturer focuses on advanced fabrication techniques, strict quality control, and compliance with global safety standards. This ensures that each needle meets the necessary medical-grade specifications. In this blog, we will explore why precision engineering is non-negotiable in meso needle manufacturing and how it impacts overall treatment outcomes.
What is Precision Engineering in Meso Needle Manufacturing?
Definition of Precision Engineering in Medical-Grade Needles
Precision engineering refers to the meticulous design and manufacturing process that ensures each needle meets strict tolerances in sharpness, length, gauge, and material composition. This high level of accuracy is crucial in medical and aesthetic applications where consistency directly impacts treatment results.
How Microscopic Accuracy Enhances Meso Needles
Meso needles are designed for minimal invasiveness and maximum effectiveness. A difference of just a few microns in needle diameter or tip sharpness can determine whether a treatment is comfortable and effective or painful and inefficient. Microscopic precision in the manufacturing process ensures:
Uniform penetration depth for accurate delivery of active ingredients.
Reduced skin trauma, leading to quicker healing times.
Enhanced treatment consistency across multiple applications.
The Relationship Between Needle Sharpness, Length, and Gauge
Sharpness: Ultra-sharp meso needles minimize discomfort and ensure seamless ingredient delivery.
Length: Different treatments require varying needle lengths, from 0.5mm for superficial applications to 4mm for deeper penetration.
Gauge: Thinner needles (higher gauge) allow for less invasive procedures, while thicker needles (lower gauge) are used for more substantial injections.
The Key Components of Precision in Meso Needle Manufacturing
Material Selection: Medical-Grade Stainless Steel vs. Alternative Materials
The choice of material is a critical factor in meso needle manufacturing. High-quality medical-grade stainless steel is the preferred material due to its:
Corrosion resistance, preventing contamination during treatments.
Durability, ensuring the needle does not bend or break easily.
Biocompatibility, minimizing allergic reactions or adverse effects on the skin.
Micro-Fabrication Techniques: CNC Machining, Laser Cutting, and Electro-Polishing
Leading meso needle manufacturers leverage advanced micro-fabrication techniques to ensure precision:
CNC (Computer Numerical Control) Machining: Allows for highly accurate shaping of needles with minimal deviation.
Laser Cutting: Ensures clean, precise edges and ultra-sharp tips.
Electro-Polishing: Enhances needle smoothness, reducing resistance during injection and improving patient comfort.
Consistent Needle Diameter & Gauge: Ensuring Uniform Penetration Depth
Precision-engineered needles maintain a consistent gauge and diameter, allowing for uniform penetration depth and predictable treatment results. This prevents:
Inconsistent ingredient distribution.
Uneven healing and post-treatment discomfort.
Ultra-Sharp Needle Tips: Minimizing Patient Discomfort
The beveling and polishing process ensures meso needles have ultra-sharp tips, leading to:
Easier penetration with minimal pain.
Lower risk of tissue damage.
Improved overall patient experience and satisfaction.
Why Precision Matters: The Impact on Safety and Effectiveness
Reduced Pain and Trauma: Enhancing Patient Comfort
A finely engineered meso needle ensures:
Minimal resistance when penetrating the skin.
Less bruising and redness, improving post-treatment recovery.
Higher patient satisfaction, encouraging repeat treatments.
Better Delivery of Active Ingredients
Meso needles are designed for optimal infusion of serums and active compounds, ensuring that:
Ingredients are delivered to the correct skin layer for maximum efficacy.
There is minimal wastage of expensive formulations.
Treatments achieve consistent results every time.
Minimized Risk of Skin Damage or Infection
Precision in sterility and needle smoothness helps prevent:
Tissue tearing due to irregular needle tips.
Infections caused by poor-quality materials or improper sterilization.
Adverse skin reactions, ensuring patient safety.
Durability and Breakage Resistance: The Role of Advanced Manufacturing Techniques
Poorly manufactured needles may break, bend, or dull quickly. High-quality precision-engineered meso needles offer:
Greater structural integrity, preventing accidental breakage.
Long-lasting sharpness, ensuring consistent results over multiple uses.
Advanced Technologies Used by Leading Meso Needle Manufacturers
Robotic Precision Cutting & Grinding: Eliminating Human Error
Modern meso needle manufacturers use robotic cutting and grinding to ensure:
Absolute precision in needle dimensions.
Elimination of human inconsistencies, leading to higher-quality production.
Automated sharpening for superior penetration capabilities.
Automated Quality Control Systems: AI-Driven Defect Detection
Artificial Intelligence (AI) plays a crucial role in quality control. Automated high-resolution imaging and machine learning algorithms detect:
Microscopic defects in needle tips and bodies.
Variations in gauge or length, preventing faulty products from reaching the market.
Sterilization & Packaging Innovations: Ensuring Compliance with Global Safety Standards
Sterilization techniques, such as ethylene oxide gas and gamma radiation, ensure that each meso needle is 100% free from contamination. High-quality packaging solutions maintain sterility and prevent damage during shipping.
Certifications & Compliance: The Hallmark of a Trusted Meso Needle Manufacturer
ISO 13485 Certification: Ensuring Medical Device Quality Standards
ISO 13485 certification indicates that a manufacturer follows internationally recognized medical device quality standards, ensuring safety, reliability, and consistency.
CE & FDA Compliance: Guaranteeing Safety for Global Markets
A reputable meso needle manufacturer must adhere to CE (Europe) and FDA (USA) regulations, ensuring:
Compliance with strict health and safety protocols.
Approval for use in medical and aesthetic procedures worldwide.
Sterile Processing & Biocompatibility Testing
Needles must undergo biocompatibility testing to confirm that materials are safe for human use. This includes:
Endotoxin testing to prevent bacterial contamination.
Heavy metal analysis to ensure material purity.
Choosing the Right Meso Needle Manufacturer: What to Look For
Manufacturing Experience & Expertise
A well-established meso needle manufacturer with years of experience guarantees:
Proven track record of quality and innovation.
Strong research and development (R&D) capabilities.
Quality Control Measures
Top manufacturers implement:
Multi-stage inspections to catch defects early.
Randomized product testing to ensure batch consistency.
Customer Support & Customization Options
A trusted manufacturer provides:
Custom branding and packaging for distributors.
Technical support for clinics and professionals.
Bulk ordering options with competitive pricing.
Conclusion
Precision engineering is the backbone of high-quality meso needle manufacturing. From material selection to micro-fabrication techniques, robotic precision, and stringent quality control, every step impacts the safety and effectiveness of meso needles.
Choosing a reputable meso needle manufacturer ensures superior treatment outcomes, enhanced patient comfort, and long-term reliability. For clinics, distributors, and aesthetic brands, investing in precision-engineered meso needles is essential for delivering consistent, high-quality results.
If you're looking for a trusted meso needle manufacturer, prioritize quality, certifications, and innovation to ensure the best experience for your clients and patients.